► Continental’s Richard Durance talks tyres
► The future of tyre materials and design
► How different compounds make a difference
> Continental started out by rubber-skimming aircraft wings in the early 1900s. Now we have 205,000 employees in 53 countries and annual sales worth €34.5 billion. Only 28% of the business relates to tyres, and much of the remainder is brake systems, chassis technology and stability control systems.
> Our Black Chili compound was originally developed for bicycle tyres in 2005. It’s a special polymer combined with other raw materials, and was first used on the ContiSportContact 5 in 2010. It adjusts to the surface and keys into grip, helping to force away water. Black Chili also uses small suction pads like geckos’ feet; they’re microscopic.
> We can tune each tyre for individual OEMs, so even though two tyres might look identical, each can be specific to a certain car. The steel belt, ply material, apex and reinforcements in the bead area can all be tuned, and it has a big effect on how forces are transmitted, as well as the compromise between comfort and steering response. For instance, we can make the apex in the bead area taller, which increases steering response, but sacrifices comfort. Make it smaller and the reverse is true. It’s all about finding that compromise.
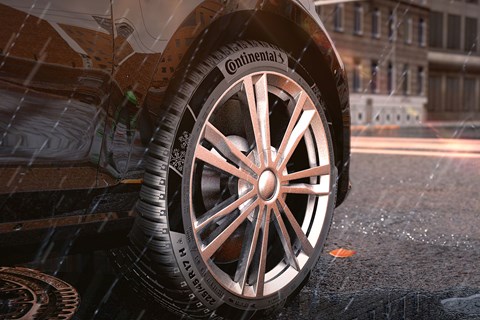
> We are investigating how we can manufacture tyres from dandelions. It involves refining the latex we require from the stalk. It’s too early to say if these tyres would give us the correct properties, and I’m not sure on yield per acre, but it will reduce the amount of synthetic oil required.
> There are three conflicts to tyre performance: rolling resistance, wet performance, and wear. If you improve wet performance by 2-3%, the tyre might wear 15% faster. Tyre life has improved over the last couple of decades, but you have to consider how both vehicle dynamics and performance have improved. Tyres are now asked to do a lot more, even though we’re not always conscious of it.
> Tyre compound accounts for 50% of rolling resistance. No-one wants to compromise on other factors while decreasing rolling resistance. In fact, we’ve improved rolling resistance by 20-30% since the 1980s, despite larger, wider tyres, but I think a 2% per year improvement is the limit. We’re trying to achieve even lower rolling resistance for electric cars.
> A tyre’s compound is so important to safety and performance, it’s not just about the tread pattern. A Chinese company copied our tread pattern exactly, and we did tests to show that the stopping distance was massively longer.
> We are looking at different polymers for run-flat tyres that react intelligently when put in a different load environment. For instance, a sidewall that can flex to give good handling, comfort and low rolling resistance when fully inflated, but the characteristics change to create a much stiffer sidewall in the event of tyre pressure loss. So you get the advantages of run-flat technology while minimising any negative attributes.’
Read more from CAR magazine